2 мифа о газификации транспорта. Сеанс разоблачения
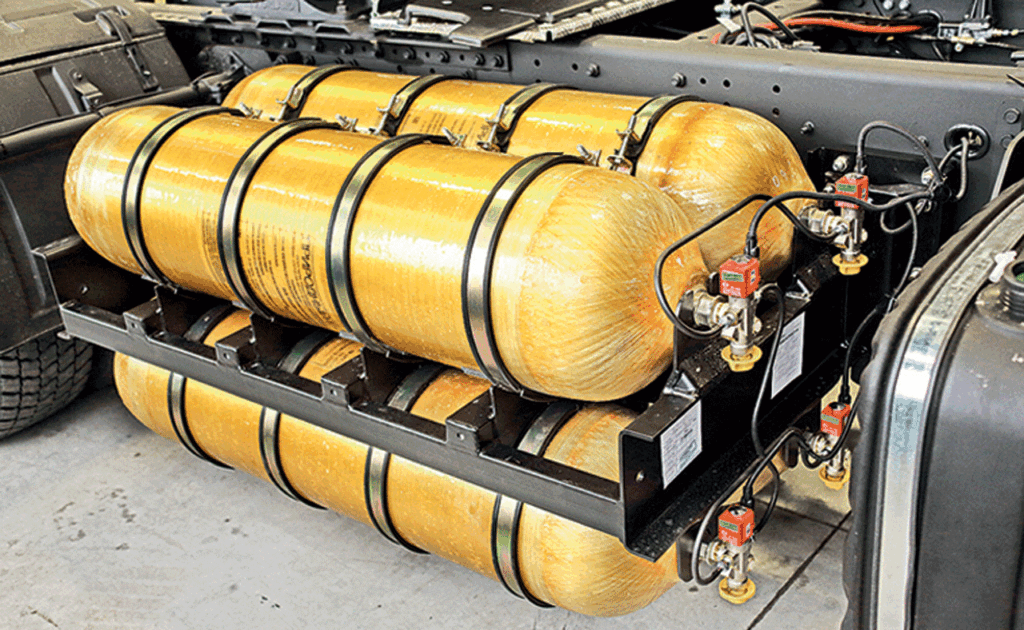
В деле газификации российского автопрома срабатывает и человеческий фактор. Если в бюджетной организации со своим автопарком привыкли «накручивать» спидометр, а потом сливать для себя бензин и солярку, то перевод автомобилей на газ там явно не вызовет энтузиазма. В основном, ужас нагоняется по следующим темам: бензиновый или дизельный мотор изначально разрабатывали не для езды на газе; газ «сушит» двигатель; существенно уменьшается ресурс – на газе «убьешь» мотор; мотор сам себя не тянет – нет той мощности; нет смысла ездить на газе – расход увеличивается почти в 1,5 раза; автомобиль с ГБО опасен в эксплуатации. Разберемся с этим обстоятельно.
Вопрос по изначальной ориентированности ДВС на бензин и дизтопливо можно задать и историкам автомобильной техники. А ответ будет таким: самые первые двигатели внутреннего сгорания были именно газовыми. В XIX столетии Бельгиец Жан Этьен Ленуар и немец Николаус Отто, работая над этой революционной для человечества темой каждый по отдельности, не располагали никаким другим топливом, кроме светильного газа. Впоследствии для обеспечения процесса испарения жидкого топлива (бензина или солярки), фактически, для перевода его в газообразное состояние, придумали карбюратор и ТНВД с форсунками. Даже устоявшийся термин «механизм газораспределения» – и тот про газ… Казалось бы, со временем все наладилось, но дефицит автомобильного топлива, рост цен на нефть не раз в ХХ веке заставляли искать альтернативу бензину. Применяли все, что горит – от спирта до древесной щепы… Поэтому немудрено, что в линейке продукции любого моторостроительного предприятия обязательно были или есть газовые двигатели, созданные обычно на основе бензиновых моторов или конвертированные из дизелей.
Газ «сушит» двигатель
К вопросу о том, что газ «сушит» двигатель. Даже по терминологии понятно, что он из разряда шоферских баек. Когда спрашиваешь, что же в моторе больше всего подвержено «усушке», внятный ответ получить невозможно. Хотя в этом слове из водительского жаргона есть и рациональное зерно – так говорят об уменьшении ресурса мотора. Да, среди российских автомобилистов бытует мнение, что от газа подгорают выпускные клапаны и седла. Но в основном этот негативный опыт от перевода советских легковых автомобилей на пропан, причем без корректировки установки момента зажигания, без учета качественного состава рабочей смеси. Еще один важный момент. На тех же «Москвичах», «Жигулях» и «Волгах» не применялись выпускные клапаны с натриевым наполнителем в «ноге», как на V8 семейства ГАЗ 53. Не использовался и механизм проворачивания выпускного клапана, как на моторах ЗИЛ 130/375. А эти решения увеличивали ресурс клапанов!
Газ «убивает» мотор
На современных, специально разработанных газовых двигателях, и даже на конвертированных из бензиновых и дизельных моторах, применяют особые жаропрочные стали для клапанов и жаропрочный чугун для седел. Кроме того, сами чугунные головки блока более долговечные, чем головки из алюминиевого сплава. Повторимся, на советских легковушках ничего этого не было. И даже если через 70-100 тысяч километров пробега на газе (а то и больше!) приходилось снимать головку и шарошить-притирать клапаны, то экономия все равно была очень заметная.
Если вскрыть головку мотора, долго работавшего на газе, то легко убедиться в минимальном износе поршневой группы. На цилиндрах хорошо сохраняется хонинговальная сетка, зазор в стыке поршневых колец в пределах допуска, зазор между «юбкой» поршня и гильзой тоже без претензий. Объяснение тому простое – газ не смывает масляную пленку с поверхности цилиндров. Не увидеть на газовом моторе и детонационных разрушений поршней и колец.
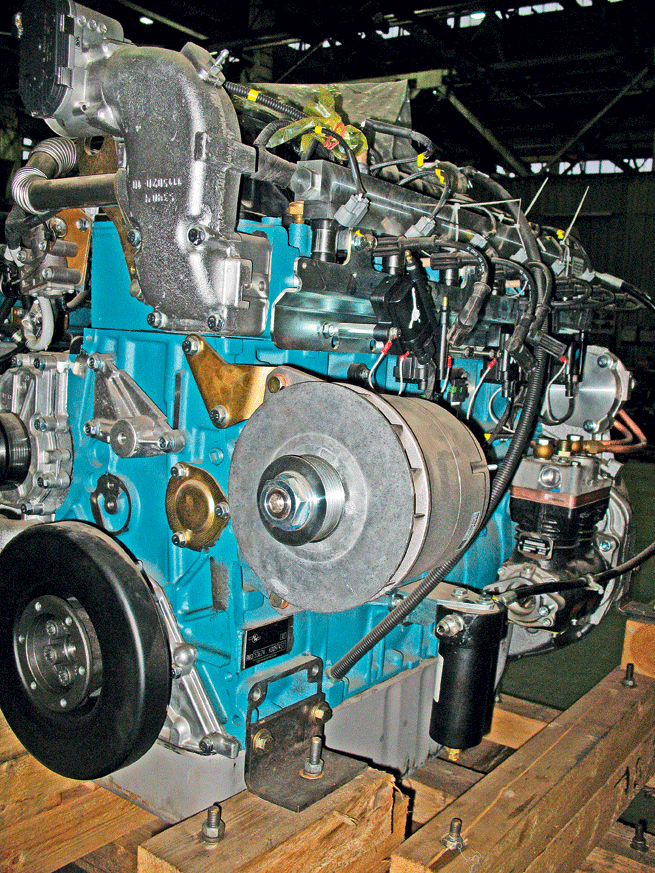
Если говорить о конвертированных моторах из дизеля в газовый, переведенных на цикл Отто, то там степень сжатия не 16-17 единиц, как обычно на дизеле с турбонаддувом, а всего 11-12. Для этого изменяют поршни, именно в них находится камера сгорания. У газовых моторов есть весьма сложная зависимость степени сжатия от применяемого газа – с его метановым (не цетановым, и не октановым) числом – от диаметра поршня, формы камеры сгорания. Большой эффект дает применение микропроцессорных систем зажигания и датчиков детонации – двигатели работают без разрушительного «звона пальцев». Для поршней применяют более жаропрочный, чем для дизеля, алюминиевый сплав, часто легированный медью и никелем. Поршни для газового мотора могут быть снабжены специальным каналом для принудительного охлаждения маслом. Кроме того, остаются и обычные форсунки для впрыска масла во внутреннюю полость поршня. Так улучшают охлаждение днища. У конвертированных из дизелей газовых моторов большие по размеру, чем у обычных карбюраторных двигателей шейки коленвала, более прочные блок цилиндров и шатуны, особые «дизельные» материалы и технологии упрочнения. Обычно заявленный заводом ресурс газовых моторов не ниже, чем у дизелей.
Читайте на Рейс.РФ:
Если метан самое выгодное топливо, почему его так мало?
Определено самое выгодное топливо для автомобилей
Останутся ли дизели Евро-6 на российских тягачах
Теперь нас можно читать и в Telegram
Клиенты компании «Альфа-Лизинг» до 15 июля текущего года могут приобрести любой вид автомобильной техники с выгодой из стоков компании.
Замещаем смазочные материалы ушедших с российского рынка зарубежных брендов аналогами отечественной компании ENIX
Получив официальное дилерство по маркам Foton, Sitrak и Dongfeng, компания «КОМДОРАВТО» наладила бесперебойные поставки оригинальных запчастей ко всем тягачам, самосвалам и шасси под спецнадстройки, продаваемым в России